Custom Magnesium Die Casting Service
Add Your Heading Text Here
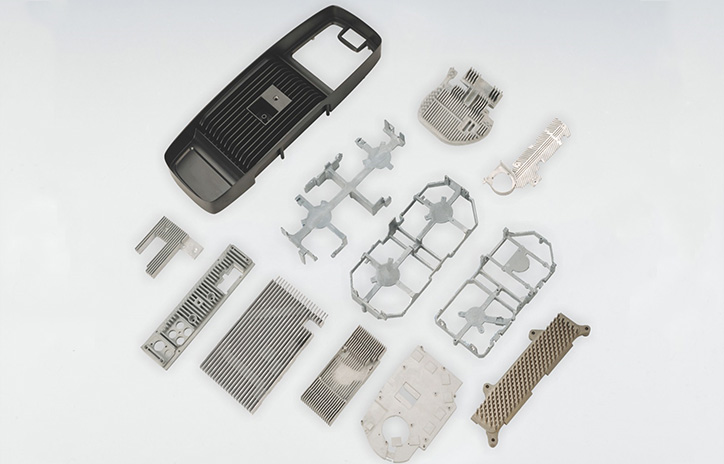
What is Magnesium Die Casting?
Magnesium die casting is a highly specialized manufacturing technique used to produce precision metal parts and components from magnesium alloy. This process involves injecting molten magnesium into a meticulously designed die or mold cavity under high pressure, enabling the creation of intricate shapes that leverage the unique properties of magnesium alloy.
Magnesium Die Casting Materials
- AZ91D: The most common alloy for high-pressure die casting. It provides a strong strength-to-weight ratio, exceptional corrosion resistance, and superior castability. This alloy is generally used for powertrain and mechanical components where toughness is prioritized over deformation capability.
- AM60B: Often used for automotive die castings for safety components like instrument panel structures and seat frames. This alloy provides very good ductility, energy-absorbing properties, strength, and castability.
- AM50: This alloy has a lower aluminum content compared to AM60. It offers enhanced ductility but slightly reduced strength and castability. It is usually used where performance requirements demand elongation properties beyond those of AM60.
Notes: There is a large selection of magnesium alloys available for applications like powertrain components operating at temperatures over 120°C (e.g., automatic transmission housing). These alloys are tailored to operate at high temperatures without “creep,” maintaining bolt tension and sealing surface flatness.
Benefits of Magnesium Die Casting
- Lightweight: 33% lighter than aluminum and 75% lighter than steel, with an excellent strength-to-weight ratio.
- Strength and Durability: Combines lightweight properties with high strength, outperforming plastics.
- Castability: Easy to machine with excellent fluidity, ideal for complex structures and thin-walled parts.
- Thermal and Electrical Conductivity: Good thermal conductivity and electromagnetic shielding, suitable for electronic components.
- Shock Absorption: Excellent vibration damping, ideal for noise and vibration reduction applications.
- Surface Quality: High surface finish, often eliminating the need for coating, with various surface treatment options available.
- Cost Efficiency: More parts per unit weight, reducing secondary processing and overall costs.
- Sustainability: 100% recyclable, supporting environmentally friendly production.
Applications of Magnesium Die Castings
Automotive: Steering wheels, seat frames, transmission cases—reducing weight and improving fuel efficiency.
Aerospace: Aircraft components—reducing weight and enhancing performance.
Electronics: Housings for electronic devices—combining lightweight properties with EMI shielding.
Industrial Equipment: Machinery parts—meeting demands for lightweight and durable components.